BEFORE THE PROJECT
• Needs analysis (the market, expectations, the company, mastering technologies)
• Solution design, budgets and planning (Preliminary project)
• Call for bids (Detailed project)
• Coordination with Civil Engineering
• Validation of maintenance choices and support for operation
• Comparison and recommendation on the choice of supplier

Optimization of the overall cost of a system
The most effective use of the overall cost of a system is during the initial phases (studies, design, development, production).
Decisions made during these phases account for a significant portion of the overall cost (upper red curve).
When the system is put into use, the optimization possibilities are very limited (dashed curve), while a significant portion of the overall cost remains to be spent (central blue curve).
DURING THE PROJECT
• Achievement of the simulation(s)
• Support and validation of the phases (Simulation, Specifications, Test cases, Reception tests; Ramp-up)
• Support in building the maintenance team (recruitment, validation of training and autonomy)
The methodology of IPMA (International Project Management Association)
https://ipma.world/ allows for the achievement of:
• Quality (functional, performance, reliability)
• Planning
• Budget
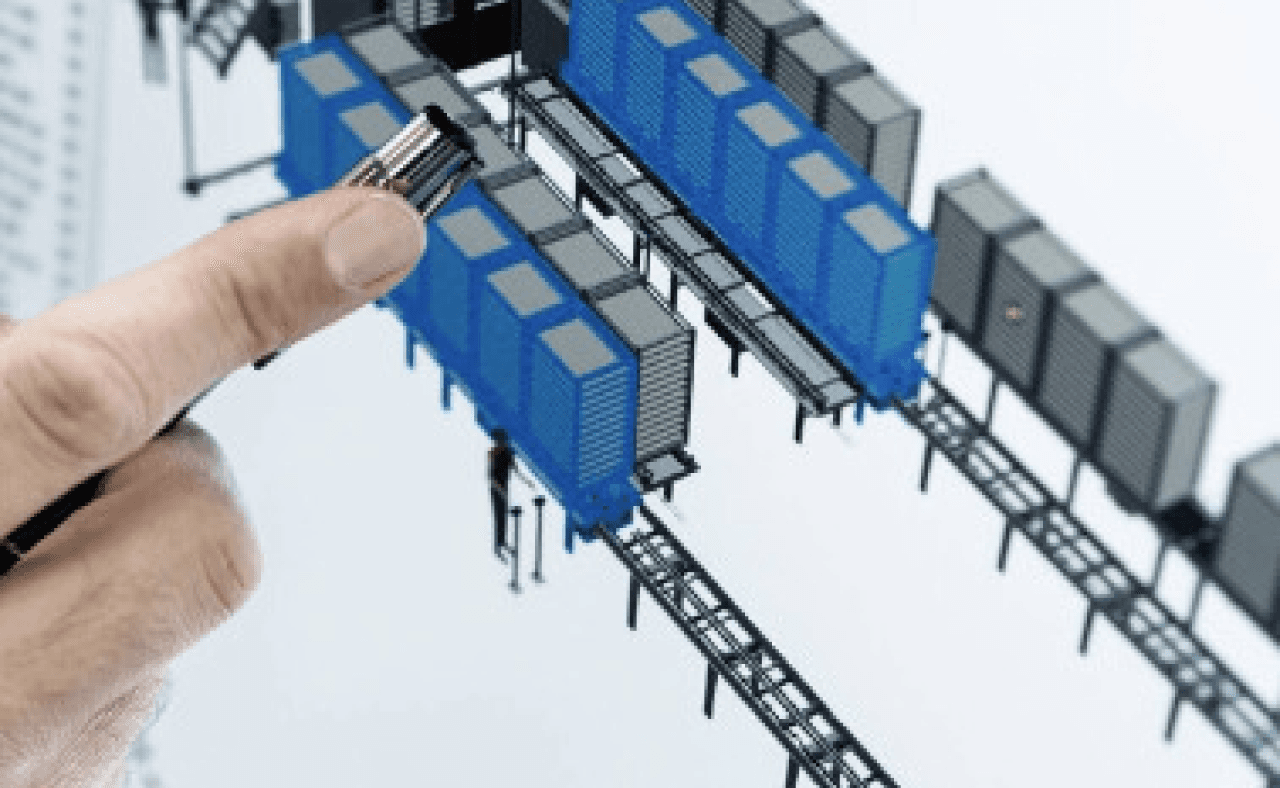
AFTER STARTUP
• Support for ramp-up
• Change management
• Audits
• Management and improvement of performance (Cost, time, quality)
• Warehouse reorganization
• Rewriting of processes and IS requirements
• Troubleshooting of an installation not meeting the objective
• Implementation of AI
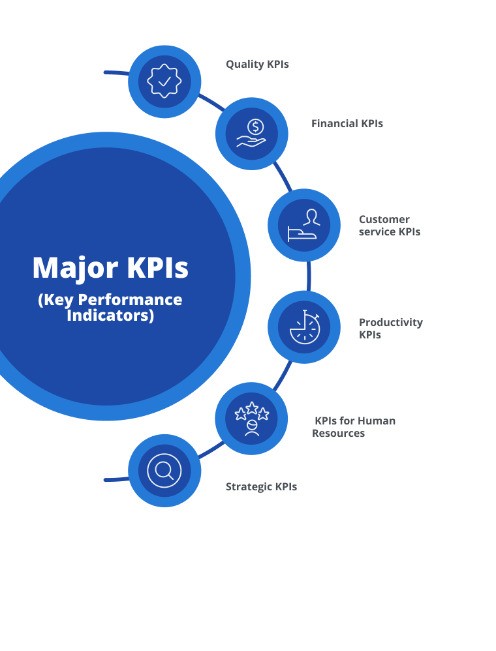
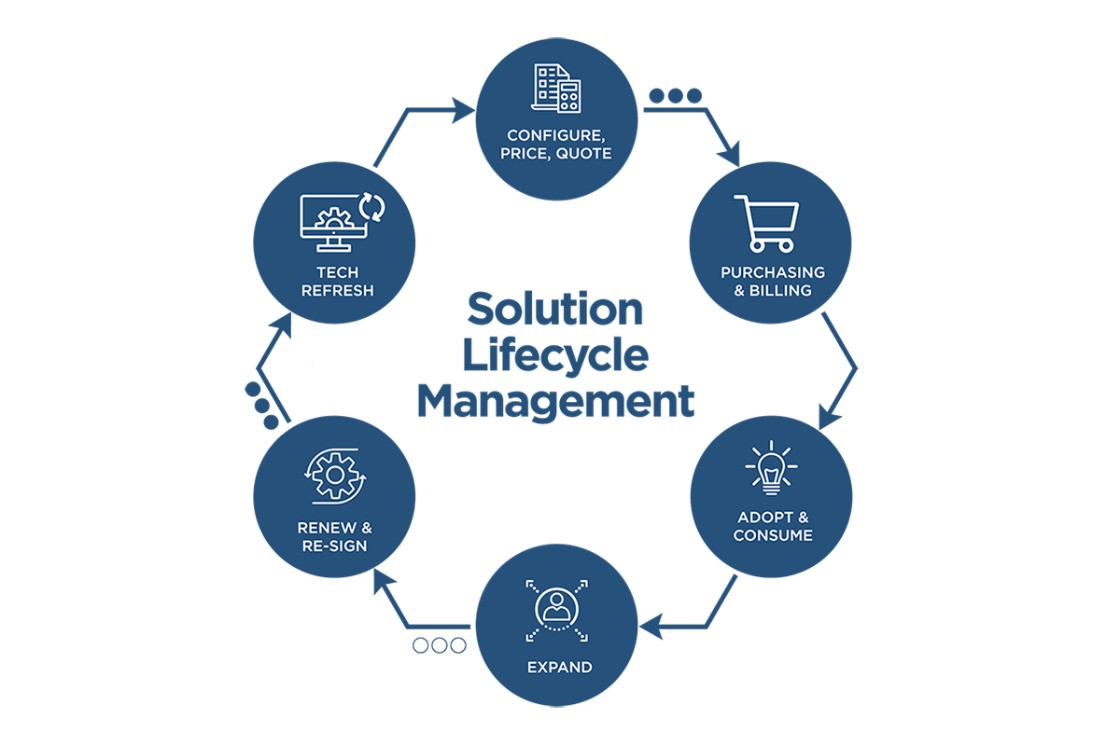
OTHERS
• Training
• Intralogistics, the right level of automation
• IPMA Methodology
• Data analysis, needs analysis
• Transition management
• Transformation support
• Recruitment of logistics experts

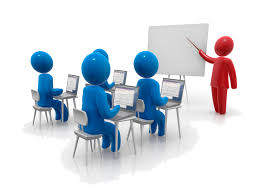
Customer requests, organizational changes, growth, staff mobility...
intralogistics solutions evolve on average every 5 years, but staff also change every 5 years in a different cycle.
Support, training, and audits help identify solutions to maintain or improve KPIs
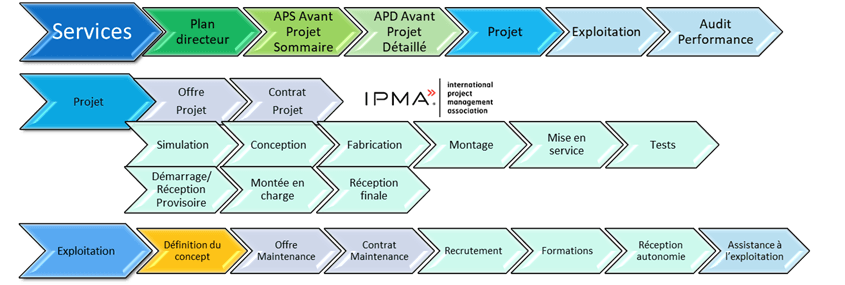